RFID Converting Machine
Enabling IoT Solutions beyond Boundaries
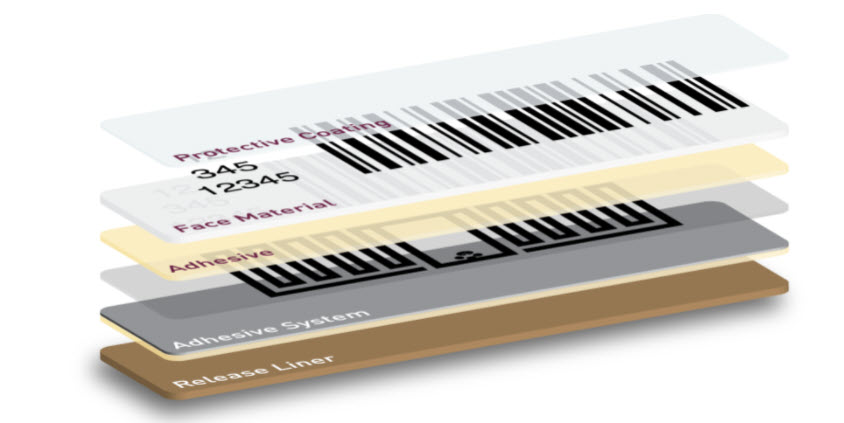
Layers of a Typical RFID Label
- Release Liner
- Bottom Adhesive
- RFID Inlay (Antenna + Chip)
- Label Material (Blank or Printed)
- (Optional) Protective Coating
More complicated RFID labels might include compensation layer for chip protection, absorption layer for pressure buffering, additional liners, conductive or dielectric layers , etc.
RFID Labels Machines
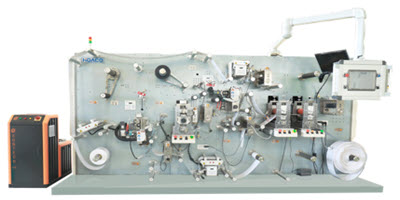
Flagship RFID Labels Machine
Purpose-built RFID machine with inline adhesive coating and inlay cut-n-transfer for cost savings.
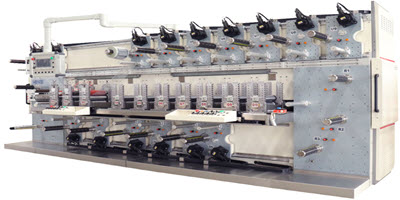
Rotary Cutting Machine for RFID Labels
Standard RDC machine for more complex RFID labels with extreme process versatility and precision
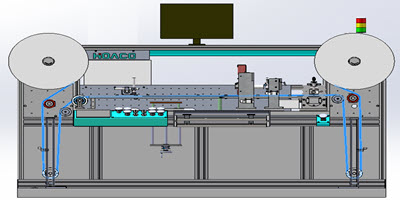
RFID Labels Inspection Machine
Perform 100% QC/QA check for RFID labels with inline black mark printing.
Flagship RFID Labels Machine
- Purpose-built RFID machine for the most economical cost savings
- Inline adhesive coating that saves liner cost of raw materials
- Vacuum-based async inlay cut-n-transfer that saves process tapes and tooling cost
- Multiple web guides for higher precision
- Solid or flexible dies for cutting label outlines
- FG in rolls, perforated or sheets
- Optional inline label reading, CCD vision inspection and defect marking
Technical Specifications | |
---|---|
Speed | Up to 70m/min |
Precision | ≤ ±1mm |
Dimension | L4500 x D1700 X H2400 mm |
Weight | 2.8 Ton |
Rated Voltage & Power | 3Phase 380Volts, 30kW |
# of Layers | 3 or 4 |
Top Label layer | Blank or Printed Label |
Bottom Liner Layer | Blank or Printed Label |
Cutting Precision | ≤ ±0.3mm |
Lamination Precision | ≤ ±0.5mm |
Max Roll Diameter | 600mm |
Max Roll Weight | 30kg |
ROtary cutting Machine for rfid labels
- Standard Rotary Die Cutting Machine for maximum versatility and precision
- Complex RFID labels of more than 4 layers can be easily handled
- Vacuum-based async inlay cut-n-transfer that saves process tapes and tooling cost
- Optional inline label reading, CCD vision inspection and defect marking
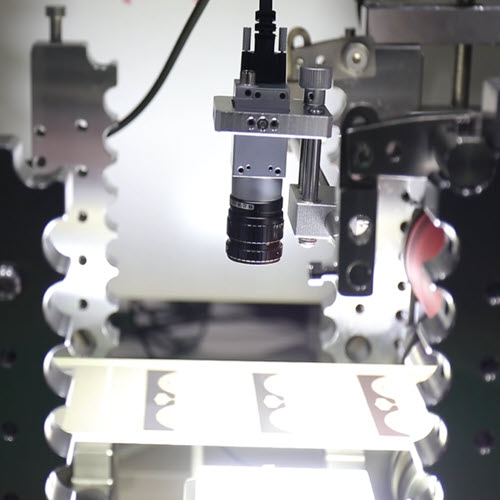
Inline RFID Reader
Connected to a single RFID controller, multiple RFID readers can be positioned optimally to perform inline RFID functional checks for optimal process control and maximize yield.

CCD Vision Inspection
Triggered by proximity or mark sensor, high-end CCD cameras captures a high-resolution motion image for visual analysis of dimensional measurement, leftover wastes, stains or misalignment.
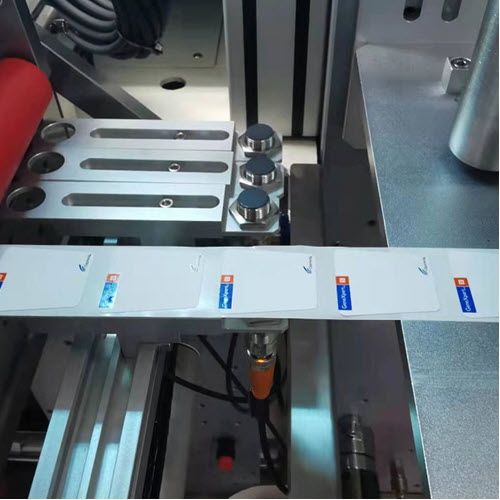
Inline Defect Marking
In the event of defective parts detected by either CCD or RFID reader, inkjet printers can be triggered to print black marks on the defects for easy quality control and analysis before shipment.
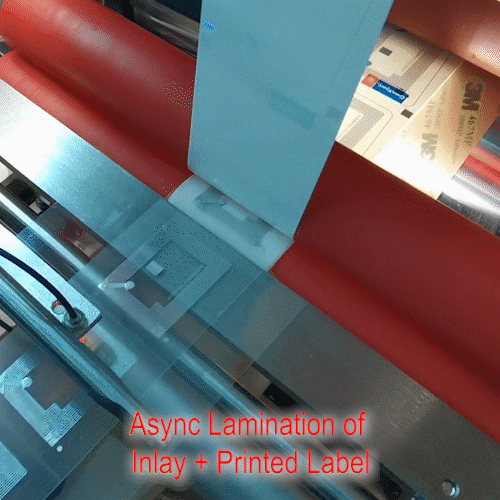
Inlay Cut-n-Transfer
Inlay cut-n-transfer can be realized through async lamination or vacuum-based cut-n-transfer. The former requires supporting process tapes but delivers ultimate lamination precision up to ±0.2mm. The latter saves process tapes and offers reasonable precision tolerence up to ±0.5mm.
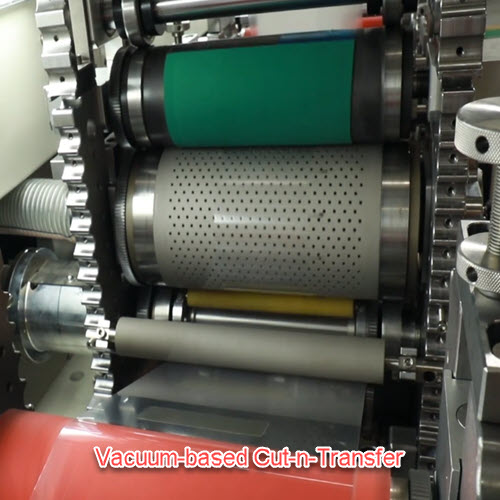
Demo Videos
Technical Specifications | |
---|---|
Speed | Up to 30m/min |
Dimension | L5200 x D1670 X H2470 mm |
Weight | 5 Ton |
Rated Voltage & Power | 3Phase 380Volts, 42kW |
# of Layers Supported | 3-6 |
Top Label layer | Blank or Printed Label |
Bottom Liner Layer | Blank or Printed Label |
Cutting Precision | ≤ ±0.05mm |
Lamination Precision | ≤ ±0.15mm |
Max Roll Diameter | 500mm |
Max Roll Weight | 25kg |
RFID Inspection Machine
- 100% RFID functional inspection for quality assurance before shipment
- Support all types of HF/UHF RFID readers and custom RFID testing software
- Automatic machine stop upon detection of defective labels to allow easy manual replacement and re-test
- Cost-effective thermal printing for defective labels
Technical Specifications | |
---|---|
Speed | Up to 300 labels/min |
Dimension | L2300*D1300 * H1700 mm |
Weight | 0.8 Ton |
Rated Voltage & Power | Single Phase 380Volts, 6kW |
RFID Reader Interface | USB or RS232 |
Defect Marking | Thermal Printer |
Max Roll Diameter | 600mm |